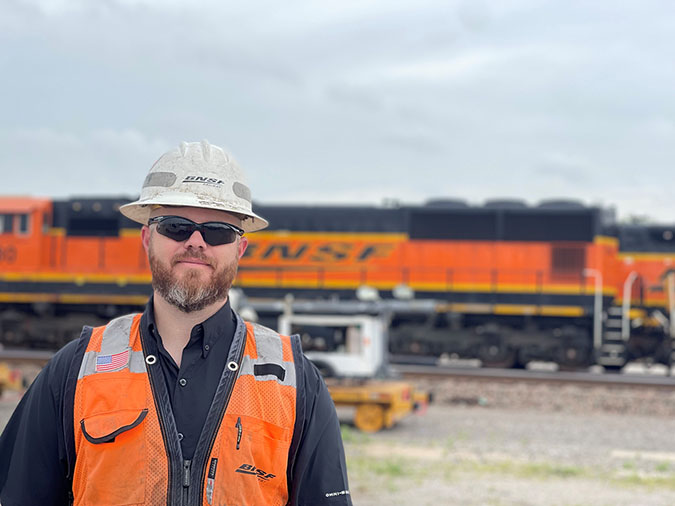
A day in the life of a BNSF track inspector
By EUNICE ARCHILA
Staff Writer
It’s 9 a.m. on a Tuesday in June. BNSF’s Gainesville, Texas, yard office is quiet, tucked in the heart of the terminal. Inside, benches, tables and computers line the room. A fresh pot of coffee brews as BNSF employees trickle in, stowing away essentials in lockers and chatting about weekend plans. The low hum of radio transmissions and the distant rumble of passing trains bring the building to life.
But long before the first cup of coffee is poured, the workday has already begun.
Track Supervisor Jesse Cunningham starts his day at 6 a.m. with a daily conference call that includes the roadmaster, track section employees, welders and teams from two subdivisions. The call covers safety briefings, daily assignments and lessons learned across the network.
“If any recent safety incidents occurred, we’re going to talk through it—how it happened and what to look out for to avoid doing the same,” Cunningham said. “We also talk through the weather’s impact on the rails and any special projects we’re working on.”
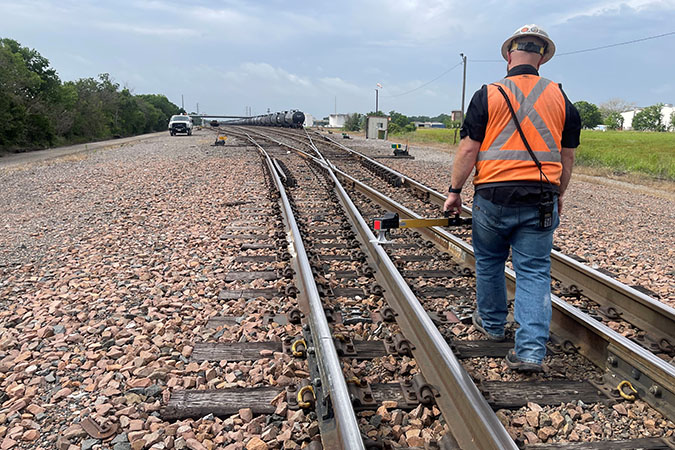
As one of hundreds of track inspectors at BNSF, Cunningham’s job is to ensure that his territory of track, including mainlines, sidings and yards, is safe and in good condition. He and his colleagues inspect to identify track defects, wear and tear, misalignment and other potential issues, then help develop repair plans and source the necessary materials to keep the tracks in top shape. Using data from inspection vehicles increasingly plays a role in how he accomplishes the task.
Cunningham conducts his track inspections twice a week— three times if a recent geometry car detected a defect. These specialized track geometry cars, or “geo cars,” are equipped with sensors that measure and record the health of the track, identifying defects and surface conditions that may not be visible to the naked eye.
This technology has transformed the role of track inspectors. “We used to hyrail and walk the track four days a week,” Cunningham said. “Now, with the help of geo cars, we can focus our time where it’s needed most.”
Using geo cars, we were able to inspect more than 500,000 miles of track last year. To increase inspections and data gathered even further, we’ve developed a locomotive-based track geometry system that will dramatically increase the miles inspected as freight moves across our network. Working in concert, the technology will allow inspectors to address potential risks proactively, shifting from finders to fixers.
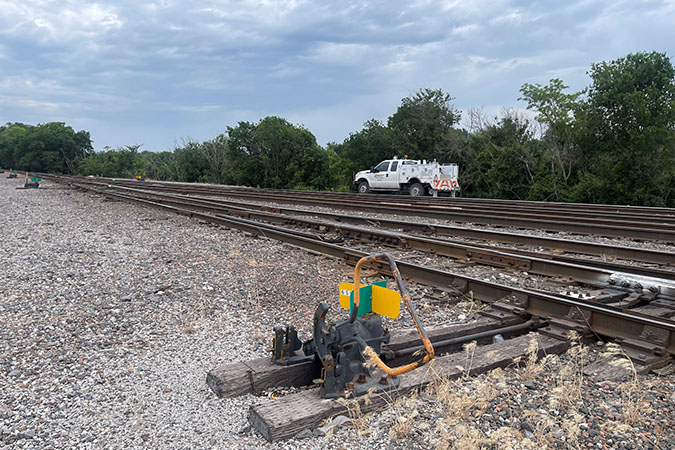
On a typical day, Cunningham inspects five to 10 switches, relying on both technology and hands-on experience. He follows the FRA track safety standards and leverages technologies like Vehicle Track Interaction, which uses sensors to monitor track and trains, geo cars, and DCAR (rail detector cars) data to assess track health.
“You can look at a picture of a track and it won’t look too bad,” he said. “But in person, you can step on a railroad tie and feel and hear that the wood is hollow. Sometimes they look new on top, but underneath, they’re shot.” That blend of human insight and advanced tools is critical. Both people and technology can fail. But together, they’re a powerhouse.
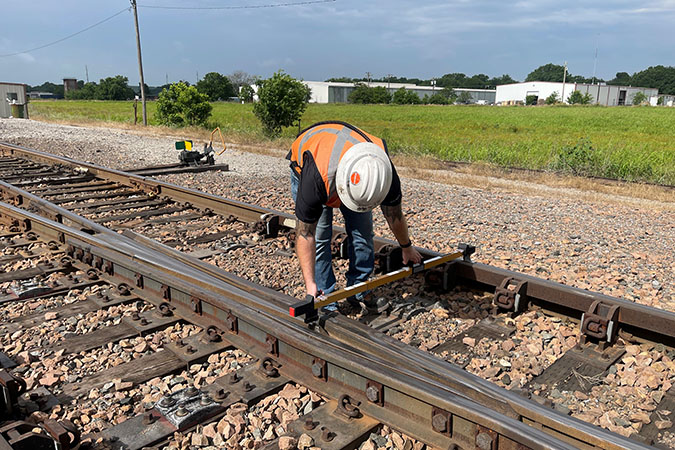
While geo cars, onboard systems, and X-ray tools provide deeper insight into track health, our people are still integral as they use that data and their on-the-ground experience to safeguard railroad operations around the clock.
“It’s not a 9-to-5 job,” Cunningham said. “You could be out here until 9 p.m. for heat inspections, then get a call at 2 a.m. for a flash flood. It’s better when the weather’s steady, but we’re ready for anything.”
Inspectors also work closely with dispatchers to coordinate safe access to the track. Using tools like the Smart Mobile Client they can monitor train locations in real time and request clearance for track protection. Once they receive the green light, inspectors can safely proceed with their track inspections.
Success, for Cunningham, is measured in prevention.
“When a geometry car runs my whole territory and doesn’t find any red tags, that’s a win,” he said. “It means we’re putting people in the right positions and doing the work before it becomes a problem.” This proactive approach is key to maintaining the safety of our tracks—for our trains, our employees, and the communities we serve.
Looking ahead, Cunningham sees the role evolving in-step with advancing technology.
Machines capture high-resolution images, X-rays, and millions of other data points, and track inspectors interpret that data and take action. By utilizing technology together with our people who know the railroad, we’re ensuring every mile of track is safe for the freight and passengers who depend on it.